The Challenges of Customizing a Cannabis Project for Medical Needs
An entire cultivation and processing procedure has to be carried out under medical standards and in highly sanitized conditions
Tal Saadon - Medical Cannabis Agronomist, LinC & Roy Peleg - Agronomist, CEO, LinC roy@lincpro.org
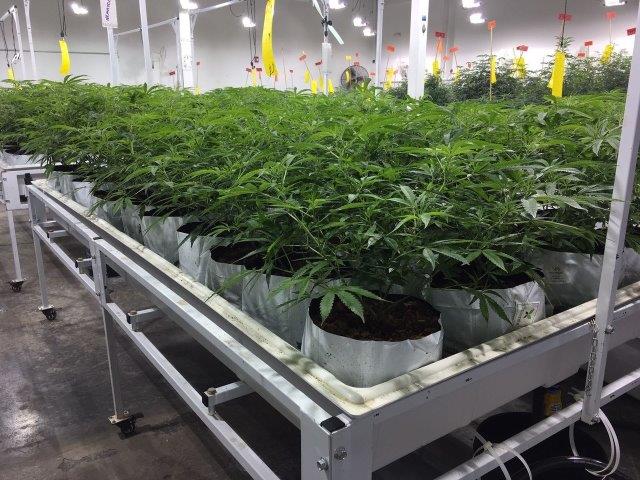
building a greenhouse facility is a complex business. it requires extensive knowledge of the crop, soil type, topography, local climate, pests and diseases, end product and economic framework. in cannabis we have two additional complexities:
first, the plant itself, which requires significant post-harvest processing: drying, curing, leaf removal and extraction.
second, the plant is cultivated for medical use, is smoked and can be used in its herbal form and not necessarily through isolated active materials, meaning that the user is more exposed to toxins and the product is harder to standardize. hence an entire cultivation and processing procedure has to be carried out under medical standards and in highly sanitized conditions.
today, medical cannabis regulation around the world varies between countries but is mostly very strict, having very low tolerance for any contamination and requires high standardization and traceability of the product and its raw materials. the most common quality standard that is used to enforce these demands is good manufacturing practices (gmp).
gmp is designed to minimize the risks involved in any pharmaceutical production that cannot be eliminated through testing the final product. gmp covers all aspects of production, from the starting materials, premises and equipment, to the training and personal hygiene of staff.
detailed written procedures are essential for each process that could affect the quality of the finished product. there must be systems which provide documented proof to ensure that the correct procedures are consistently followed at each step of the manufacturing process.
these guidelines provide minimum requirements from the manufacturer in order to assure their products are consistently high in quality, from batch to batch, suitable for their intended use.
the main purpose of gmp is to prevent any harm from occurring at the end user’s field. the main way of achieving such a result is by using high-tech greenhouses, with real-time monitoring, documentation and control over all cultivation parameters, including: light, temperature, humidity, irrigation, fertilization, pests and diseases. in the post-harvest facility, all material and work flow must be tightly controlled and standardized.
because the cultivation parameters are highly variable and depend on local climate, the selection of technology is a key factor in determining the ability of the facility, in order to meet regulation and market demands.
since the facility has to perfectly match the climatic needs, be constantly sanitized and kept free of possible pathogens and contaminants, it’s initial design is of outmost significance. without using proper design, meeting quality demands will be expensive, technically hard and sometimes completely impossible.
the preliminary characterization of the facility is the first step in achieving correct design. our characterization process begins with understanding the regulatory framework of the country in which the project is built.
we then go to the end, learning from the customer of their required product and amounts. if the cannabis will be processed for oil, then no curing or trimming of the leaves is needed and the drying could be done faster, since reducing the levels of chlorophyll is of no significance.
however, if the product will be smoked or vaped in its herbal form, then removing leaves and reducing chlorophyll levels is of great importance, as they have a dramatic effect on the product’s palatability and the overall consumption experience.
the second step in properly characterizing the facility is by providing a detailed climate and environment analysis, that includes incoming solar radiation, which enables us to know which type of cover to choose when, and how much, if at all, some supplemental lighting is needed. temperature and humidity analysis allow us to define whether we need heating, cooling and humidity control systems and their required capacity.
additional economic analysis of the technology is recommended to verify the investment economic feasibility considering the expected income. an accurate analysis will allow us to define a proper crop protection strategy for mold prevention, which is a critical step in ensuring high quality produce. in humid tropical climate, for example, we will not be able to use adiabatic cooling and will have to rely on forced ventilation and shading, to maintain temperatures. in such conditions, additional means, such as uv sterilization or resistant cultivars, will have to be considered to prevent molds.
whereas in a dry desert climate, adiabatic cooling will be the appropriate way of cooling. wind and snow loads analysis is critical for the engineering design of the greenhouse, a damaged structure due to improper design is not a pleasant sight, and more importantly will have significant impact on production capacity and the future of the farm.
the third step, after regulation and environment analysis, is planning the internal division of the facility. many projects require onsite nursery, as the availability of plants is still generally low. in such case, the division between flowering, vegetative growth, mother plantation and clone rooting must be decided according to the space requirement of each process. proper planning of the operational flow will increase labour efficiency and will prevent cross contamination.
our agronomists and experts put great emphasize on detailed and accurate specifications, providing for high quality medical cannabis production.
for more info click http://www.lincpro.org/
the article was published in #2 edition cannabis2020