The Planning, Installation and Adjustment of an Electric Sprayer Apparatus for Spraying Pineapple Grown in Greenhouses
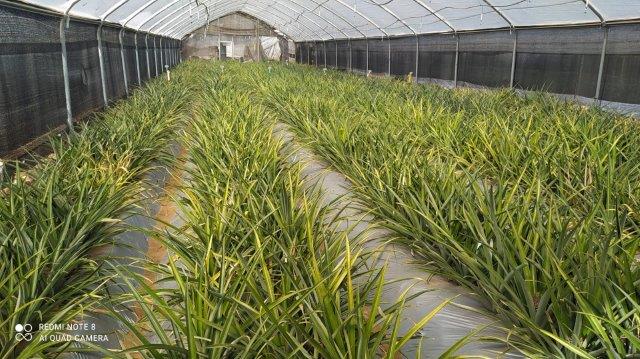
Meitav Maor (meitavm@shaham.moag.gov.il), Lior Abraham, Rafi Regev, Yiftach Afgin, Liad Reshef,
Extension service, Institute of Agricultural Engineering, Ministry of Agriculture, Israel
Ran Zadok, Pineapple Grower, Naveh, Israel;
The pineapple plant is a perennial tropical plant, the origin of which is south and central America. The beginning of pineapple cultivation in Israel took place in the 60’s, along the Sharon region. Today, pineapple cultivation in Israel is practiced by more than 100 growers on ca. 2500 dunams, the majority of which are spread along the Mediterranean coastal plain. Today, pineapple cultivation in Israel is expanding significantly, both in numbers of growers and in the number of plots.
Contrary to pineapple cultivation in the open, as is common in cultivation regions around the world, in Israel today, pineapple cultivation is practiced indoors only. This is due to the sub-optimal climate conditions: a cold winter (temperatures lower than 7°C in average) and a rainy, and a hot summer ( temperatures higher than 35°C), and dry with a strong solar radiation. The constructions used for pineapple cultivation in Israel are : greenhouses, plastic tunnels, and net (screen) houses. Under growing practices in Israel, the cultivation period from planting to harvesting lasts between 14-24 months. The planting is carried out on heightened (30cms) beds, the width of which ranges between 80 to 100 cms, 2-3 rows per bed. In the course of the pineapple plants growth, the canopy starts to cover the beds and the passages upon which the tractor moves. The canopy is prickly and relatively hardened (Photo 1a |1b), which makes the practice of manual spraying more difficult.
Photo 1: Right : manual spraying; Left : high (80-100 cms.) pineapple plants’ canopy’
The outcome of this situation is that the canopy must be trimmed, in order to let the worker with the spraying apparatus move along the passages. The above-mentioned trimming, if not done a few days before harvesting, may harm the potential yield. What’s more, due to the fact that the spraying is carried out manually, the spray dispersion on the canopy is unequal. What’s more, sometimes (e.g., in flowering boosting and nutritional sprays), there is an advantage to a spraying directed to the inside (which is partially hidden) of the plant’s canopy, a thing which is difficult to achieve while using manual spraying. In general, in pineapple cultivation, the growers are obliged to carry out different spraying treatments, e.g., nutritional sprays, various pesticide sprays, and flowering enhancement (boosting) sprays. All in all, about 20 different sprays are needed in every pineapple growth cycle.
The Aim of the Research
The planning, the developing and the upgrading of an electric platform for a spraying apparatus in pineapple cultivation inside plastic tunnels.
Methods and Materials
In the research and development plan, a few parameters were examined, with the aim of offering a possible solution for the need to spray pineapple plants growing inside plastic tunnels. Due to the fact that a pineapple plant can reach a height of 80 cms. and more, there was a need to adjust the machine/apparatus in such a way that it could move above the plants without causing any damage to the fruits or to the plants’ leaves and at the same time, spray all the plants in the range.
The first prototype developed at the Institute of Agricultural Engineering, was a mobile pineapple spraying apparatus for use inside a greenhouse (Diagram 2). The apparatus is composed of a chassis with wheels and a spraying rod, applicable for two beds. The grower has to push the apparatus along the passage in between the beds. The local grower (R. Zadok) has tested the apparatus for a few days, concluding that it is easy to operate and that its capacities were reasonable. However, he concluded that it needs upgrading to a more efficient one, so that it could cover a larger number of beds, that the worker himself be as far away from the spraying apparatus as possible and that the spraying itself be more uniform, and that the system’s chassis be higher, so that the entrance will be possible even when the plants’ canopy will be high and thus will curb the beds and the passages.
The next stage had to do with turning the electric platform (meant originally for picking vegetables and fruits), into an electric apparatus for spraying, adjusted for a passage through plastic tunnels for pineapple cultivation. A control unit was attached to the electric platform. This unit was connected to the platform by a 3.0 meter cable. A chair was added to it so that its operator could control it either by sitting on it or by walking alongside it. A spraying rod, the length of which was 9.0 meters, was installed. The rod was adjusted so that it could cover the whole width of the tunnel. A spraying tank, the volume of which was 120.0 liters was installed on the electric platform and other needed utilities. This turned the system independent, namely, with no need of an exterior water supply. In addition, the spray nozzles could be adjusted to the height of the plant, an action required in the different stages of growth.
The width of the apparatus/machine from wheel center to wheel center is 1.3 meters, its length being 2.0 meters, its turning radius being very small, so that entering a tunnel and exiting from a tunnel is made relatively easy.
Photo 2. The electric spraying device in action inside a plastic passable tunnel.
As clearly evident, it sprays in one passage all seven beds.
Results and Discussion
The experiments were carried out in a local grower’s farm (Ran Zadok). The first experimental drive of the machine was carried out without any added components or equipment. This, in order to examine its passage capacity through a sandy terrain inside the tunnel and outside it, also when it is loaded with a heavy weight. (Diagram 2). In this experiment it was evident that the machine is able to move on a sandy soil without any noticeable difficulty. The movement inside the tunnel obliged the implementation of a spraying rod of 6.0 meters. The electric sprayer was connected to a moveable spraying tank by using a tube. But when it became evident that the spray coverage was not sufficient, the spraying rod was replaced by a longer one (9.0 meters), so that all beds were under the spraying rod.
Following a few spraying runs with the machine in different gables, where the canopy size changes, it became evident that the spray reaches all seven beds. The next step was the installation of a 120-liter tank with a fuel-operated engine, on the chassis, so that it will function independently.
In the experiment described in this report, a final experimental run was carried out, where all the components added and upgraded , were examined :
The passage capacity of the machine, the run time, the spray/material dispersion on the canopy, the easiness of operation for the user, and the efficiency of opening and closing of the spraying rod upon entering and exiting from a tunnel (Photo 3).
Photo 3: A test drive of the spraying device between mulching beds without the plants’ canopy (right) and in beds with a tall plants’ canopy ( left).
The time duration of of the spraying operation by the machine from entrance to and exit from the tunnel , lasted about 8 to 10 minutes Walking along the machine and sitting on it, passed without noticeable difficulties and without any harm caused to the beds or to the plastic covers.
Summary. This study focused on the planning, the adjustments and the preparation of a spraying machine intended for working inside accessible plastic tunnels used for pineapple cultivation. Following the above-mentioned operations, already detailed in the article, the next step will take place in 2023 and will include the examination of the machine’s efficiency compared to manual spraying In the course of cultivation of pineapple.
LINK ADDRESS TO A VIDEOCLIP AND PHOTOS OF THE ELCTRIC SPRAYER IN ACTION:
https://photos.google.com/share/AF1QipP803tzzR487dTZcf3Oa0B56JnEookLibBNZzfxyX4Q-hO2Fw6pdgUpTFoS5XWOiw?key=bktyRC1Tbm8zSEtMU1oybkFtRU0wd2xCUzRPOTdB ;
Credits :
1) Rafi Regev, a member of the Institute of Agricultural Engineering and his team members Yiftach Afgin and Liad Reshef;
2) Lior Abraham, a specialist on pineapple cultivation, a member of the Israeli Extension Service;
3) Ran Zadok, pineapple grower, Naveh, Israel.
The content included in the text above is a scientific/professional text only and its content may not be used for any purposes other than scientific and/or professional ones.