SWEEPER – The first robot capable of selecting and picking ripe sweet peppers
The first generation greenhouse harvesting robots onto the market
Professor Yael Edan* yael@bgu.ac.il
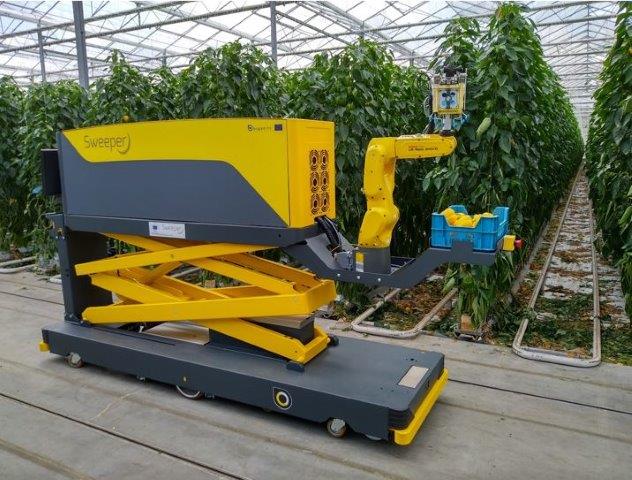
SWEEPER’s main objective was to put the first generation greenhouse harvesting robots onto the market. Until now this has never been achieved and the aim was to ensure Europe’s leading role in agricultural robotics.
The tedious manual labor involved in the harsh agricultural domain has led to shortage in manpower leading to rising demand for automation of the processes involved. This need has brought automation to almost all elements of greenhouse operation. In today’s cutting edge greenhouses all sorting, packaging and fruit transportation is performed automatically with the human serving only as a supervisor.
Harvesting is one of the few tasks that have not yet been automated. The current state of the art in automated harvesting of fruits and vegetables has remained remarkably stationary in the past decades. In the EU-FP7-project CROPS (www.crops-robots.eu) extensive research was performed on agricultural robotics. One of the applications was a sweet pepper harvesting robot.
SWEEPER a Horizon 2020 project which just concluded Oct 31, 2018 aimed to use the technology developed in CROPS to introduce, test and validate a robotic harvesting solution for sweet pepper under real-world conditions.
The project involved 6 partners from 4 different countries (The Netherlands, Belgium, Sweden and Israel). The consortium included fundamental and applied research organizations (Wageningen University & Research / Stichting Wageningen Research (NL), Umea University, Sweden, Ben-Gurion University of the Negev, Israel, Proefstationvoor de Groenteteelt – PSKW (BE)), an industrial company as system integrator (B&A Automation: – BOGAERTS (BE)) and a modern grower of sweet pepper from the Netherlands.
In the consortium a wide-range of researchers from a multitude of disciplines worked closely together along 3.5 years to produce the first commercial harvesting robot, including: horticulture, horticultural engineering, machine vision, sensing, robotics, control, intelligent systems, software architecture, system integration and greenhouse crop management.
Each of the international teams was assigned to a specific problem, and through strong continuous cooperation advanced and produced solutions that not only worked – but worked together as an integrative system. A key aspect of the development was close collaboration with horticulture experts and farmers from start and continuous testing in the greenhouse.
The researchers from the departments of industrial engineering and computer science from Ben-Gurion University led the development of computer vision and task planning algorithms for detection, localization and fruit maturity classification.
The computer science group at Umea University was responsible for high level robot control and software systems engineering; Advanced obstacle detection algorithms were developed by researchers at Wageningen Research Center who also coordinated the project and led the actual applied testing in the greenhouses.
A unique aspect of this project was the crop optimization performed by an applied research station for vegetable production in Belgium –the optimal crop for the robot and was selected along with optimizing its growth by different horticultural practices. Along the project we consulted with a Growers Advisory Board who provided plenty of good advice. All experiments were accommodated by a leading dutch grower who was an active partner. A commercial company which produces advanced greenhouse technologies dealt with the actual hardware integration and is supposed to further exploit the research results.
The agriculture environment is a very challenging environment for introducing robotics. It is highly unstructured with objects that vary in shape, size, texture, color, and location. They are also very delicate and must be handled with care. The environmental conditions continuously change (variable illumination and obstructions) and operating conditions are harsh – high density of leaves, branches, available space in between the rows is limited, and high humidity and heat.
Along the project several gripper concepts were developed and patented along with a special methodology to evaluate agriculture grippers for this complex and challenging operation. Different imaging concepts were developed and evaluated in greenhouses in the Netherlands, Belgium and Israel. New dynamic sensing and task planning concepts were developed.
An industrial robot is designed to operate in a single stem row cropping system, with a crop having non-clustered fruits and little leaf occlusion. It is placed on an automatic cart that advances autonomously along the row and thereafter travels back to the packing and sorting house with the harvested peppers.
Preliminary test results showed that by using commercially available crop modified to mimic the required conditions, the robot harvests ripe bell peppers in 24 seconds with a success rate of 61 % in a modified crop for a single-row plant stem cropping system. In laboratory experiments it was possible to harvest 1 fruit in less than 15 seconds, excluding platform movement.
Specific insights for improving performance were gathered along the many field experiments and are expected to lead to improved designs.
The project concluded with two demos in greenhouses. A first demo event was conducted on 4th of July 2018, in a commercial greenhouse. At September 12, 2018 another successful demonstration event of SWEEPER robot was conducted at the Proefstationvoor de Groenteteelt in Sint-Katelijne-Waver (Belgium)
The Sweeper robot was on display and presented during the IROS (IEEE/RSJ International Conference on Intelligent Robots and Systems) 2018 in October in Madrid.
The first robot capable of selecting and picking ripe sweet peppers is helping clear the way for a new era of agricultural robots that would change how farming in Europe is done.
For some videos see the website
http://www.sweeper-robot.eu/videoclips
* Dept. of Industrial Engineering and Management, Agricultural, Biological, Cognitive Robotics Initiative,
Ben-Gurion University of the Negev, Israel www.bgu.ac.il/abc-robotics